For almost 45 years we have been organizing and designing the interior spaces of furniture.
The Vibo products express
the ideal synthesis between
design and functionality.
45years of company history
7 plants
+1new plant for logistics and assembly
+70countries in the world
180dealers
75%export
+200employees
All is stricly
Italian-made.
Vibo accessories are closely related to the territory where they are designed, developed, and manufactured: the province of Vicenza. They proudly boast a production entirely Made in Italy, which is not just a geographical indication but also a guarantee that everything Vibo creates is aimed at the pursuit of quality to improve people's lives.
All is strictly under our direct control.
Our commitment to improvement has led us to refine our production management techniques as well. Since 2015, we have been adopting the Lean Production philosophy, which aims at minimizing warehouse stock in order to reduce the waste of resources. The adoption of a lean philosophy, on the one hand, has reduced our environmental impact, and on the other, allowed us to clearly and precisely trace our production flow. All this has also improved the management of any product or process non-conformities.
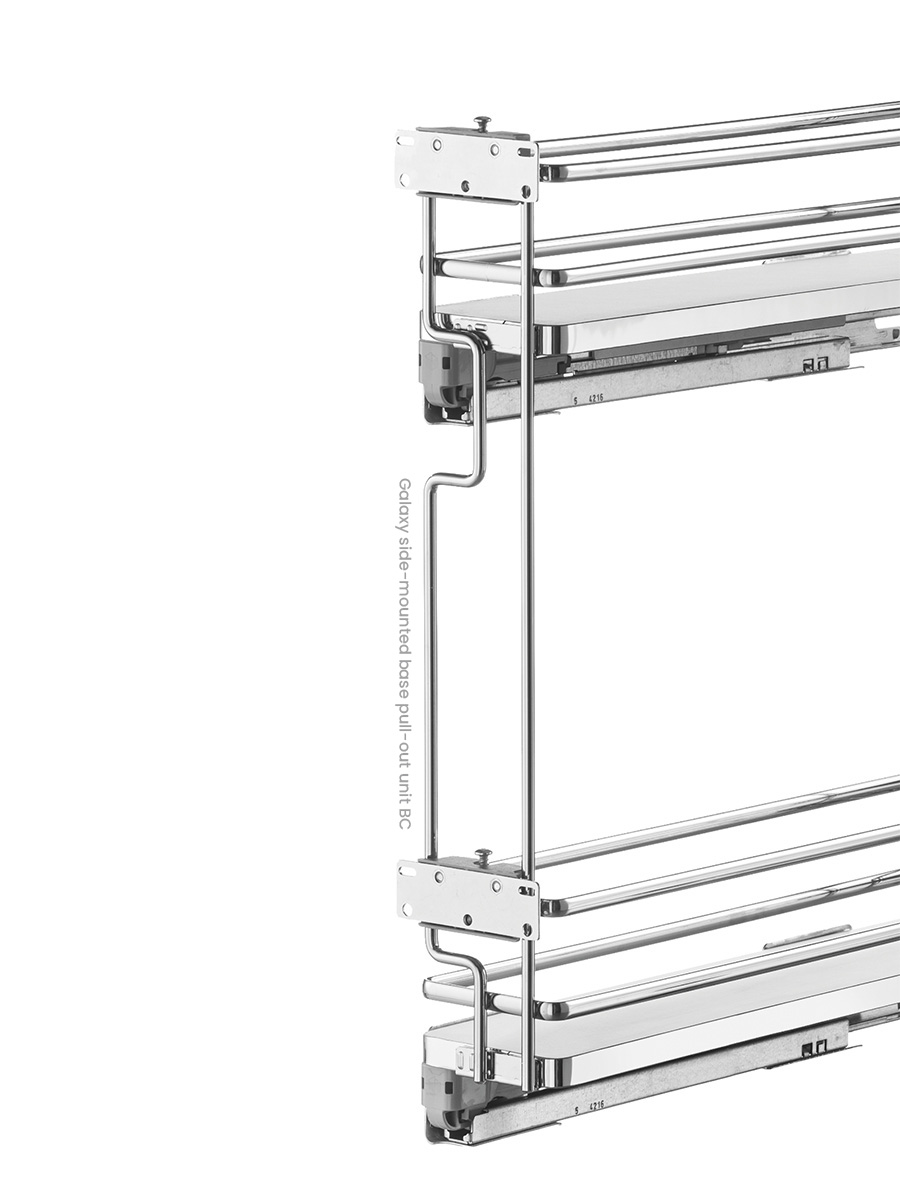
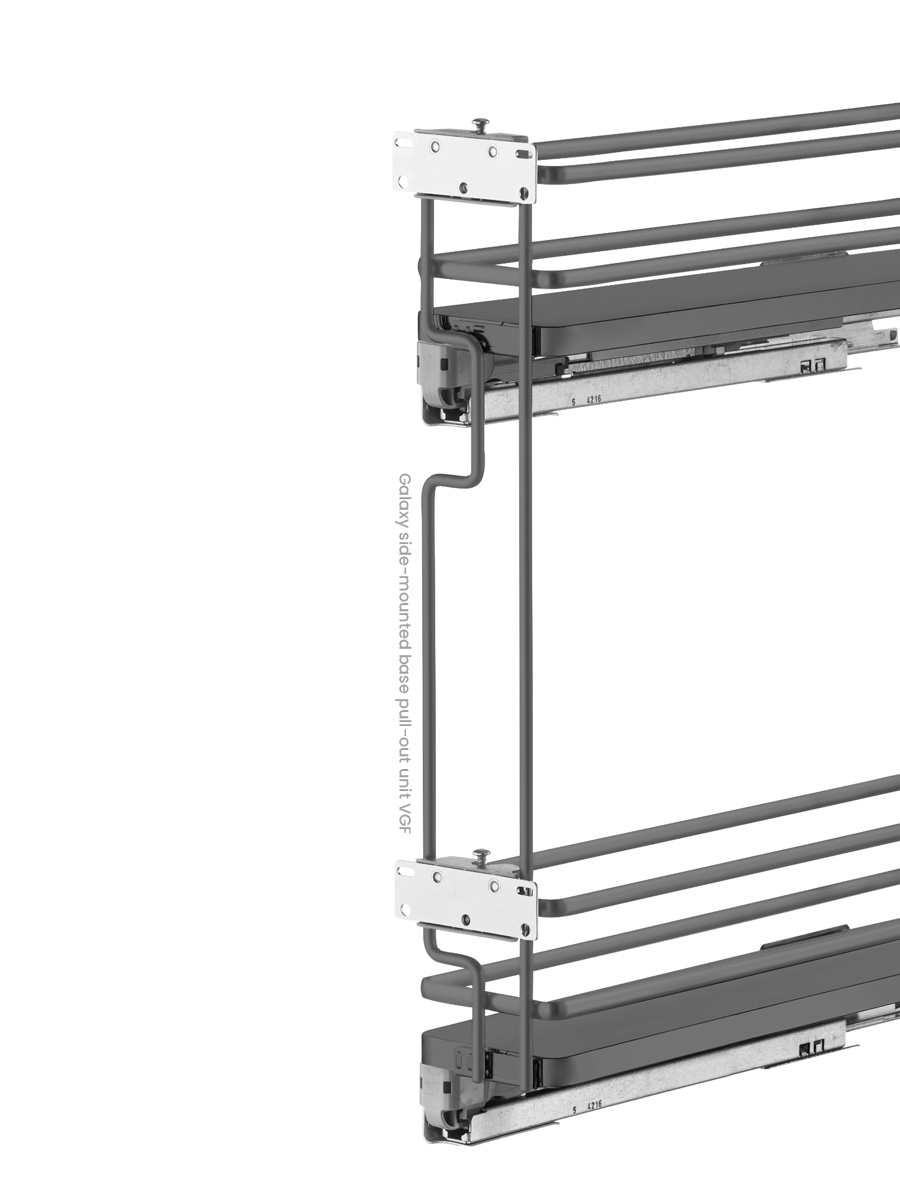